PLC Upgrade: The pros outweigh the cons
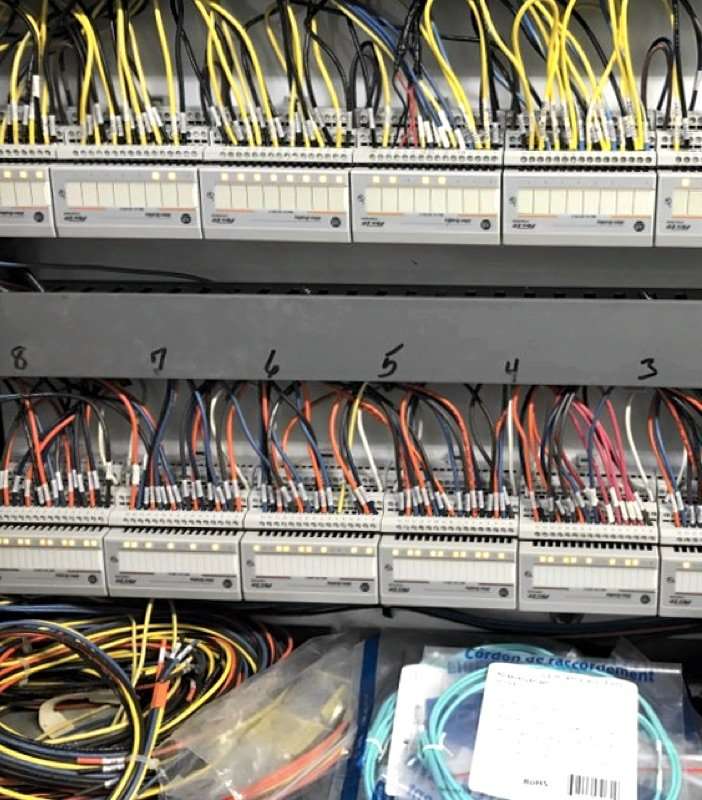
The Peak Materials migration from GE PLC to Allen-Bradley
About three years ago, Peak Materials decided to take matters into their own hands. The Colorado-based supplier of industrial ready-mix concrete, asphalt, and other aggregates had been in business for more than half a century. But they were hearing from other companies in the industry that the GE PLCs that Peak had been using in their equipment for decades were not ideally suited for this line of work and were becoming increasingly problematic to service and support.
Coincidentally, it was around this time that Peak received a call from Quantum Solutions Inc. (QSI), checking in on whether Peak was happy with their current PLCs. After some discussion, an in-person assessment, and a subsequent quoting process, Peak hired QSI to tackle a full conversion from a GE PLC and 2 remote IO racks to the more modern Allen-Bradley 5570 CompactLogix PLC.
Challenges in the Mountains

The outdated GE PLCs used a couple of remote racks located in different parts of the quarry-like complex. In order to complete this conversion, QSI needed to communicate with those racks from the main hub. In a typical conversion, the engineers would simply connect via hardwired Ethernet/IP communications, but it was clear from the outset that the distance between points was too far for Ethernet. Therefore, the original proposal called for the use of radio communication using wireless Ethernet radios. But now that QSI was on the ground, their engineers’ concern grew that the heaps of rock and dirt dotting the landscape—some as tall as 50 feet—might obstruct the antenna communications.
A quick pivot to beat the clock
Fortunately, QSI’s engineers quickly came up with a new plan on site. The engineers decided to run fiber-optic cable through the same conduits that much of the old GE cables were running through. This use of fiber was still new to the QSI engineers, but they had done their homework for just such an occasion. After having to use a welding torch to thaw the metal conduit that held the old cable still frozen in the ground, QSI engineers worked with a long-bearded independent local electrician named Ray that Peak had brought in to pull the fiber and proceed with the conversion as planned.
Finished with time to spare
On Wednesday, QSI engineers observed as each system began running smoothly and sequentially under the new Allen-Bradley PLC. The engineers walked through and tested each point of input and output. Along the way, they were able to explain the new systems to the Peak employees that would go on to run and monitor them. By Thursday, the rock crushing and mountain building had commenced.
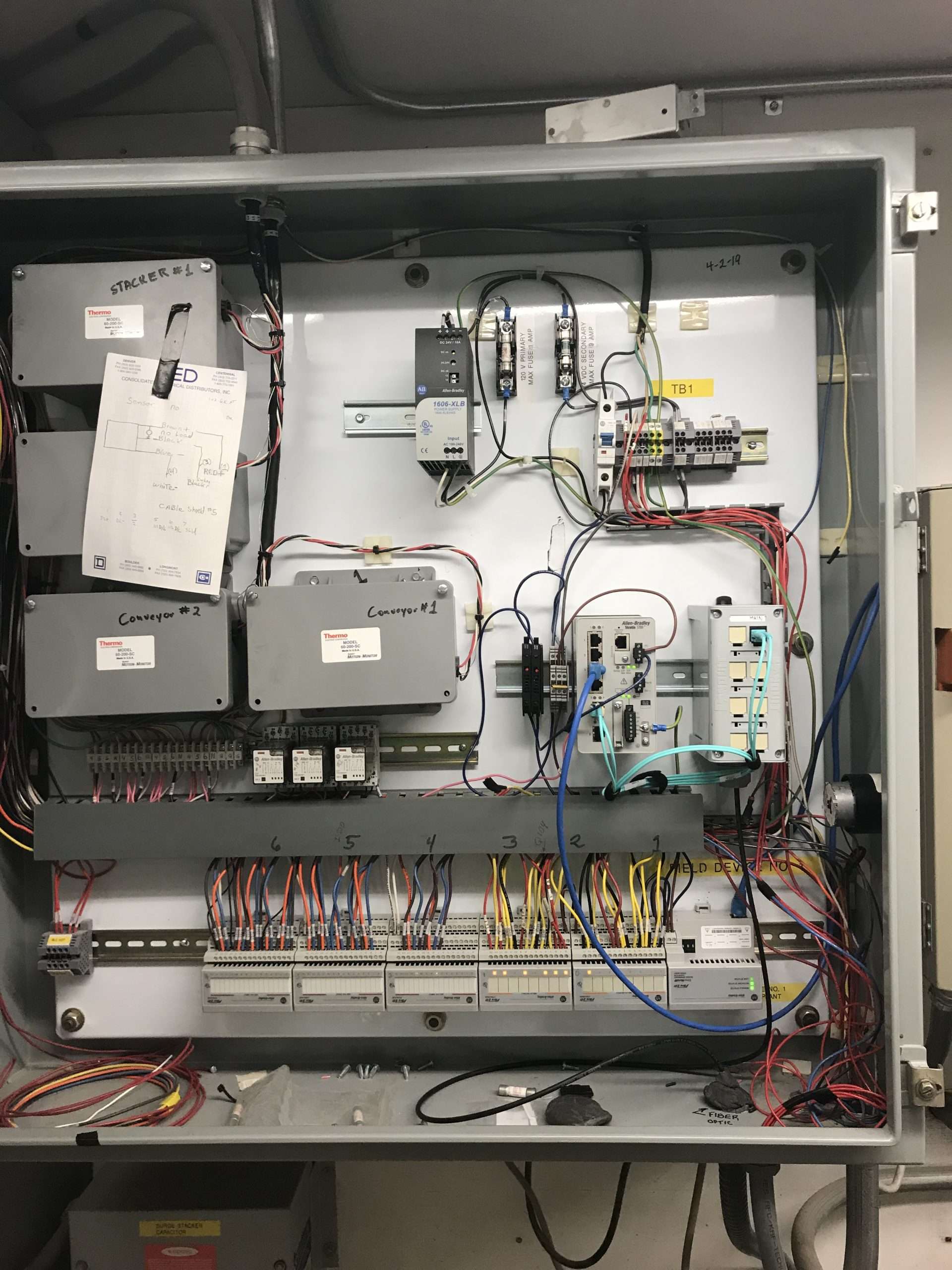
An extra day and a bonus job
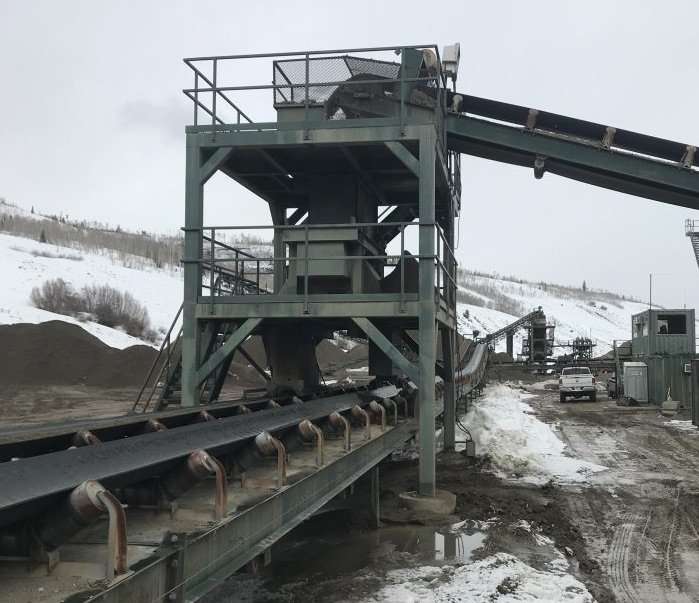
While onsite, the Peak main control room suddenly lost communications with one of the outlying offices. Since they were there anyway, QSI engineers teamed up with the Peak IT team to troubleshoot and resolve the issue.
Always there when needed
Typically, a conversion the size of this is a once-every-couple-decades expense for a company like Peak. And now that they’re running a state-of-the-art Allen-Bradley PLC and back crushing stone and cranking out concrete and asphalt, the Colorado firm is better prepared for expansion and growth. They likely won’t have much regular need of QSI’s services in the near future.
But as far as QSI is concerned, that isn’t the point. They were brought in to do a job and they performed beyond expectations in terms of both scope and timeframe. In the process, they got to know more about Peak’s industry and came to feel like a part of the team. The engineers also developed new tools and skills that they’ll be able to put to work for future clients, whether it’s Peak or another company in need.